Flight Simulator Hardware is the back-bone of a Full Flight Simulator. Our tailor-made frames literally hold all the pieces together. As such, they transform the forces and accelerations of the motion systems which are mounted on the frame itself.
A few examples of the products we manufacture are frames, or upper platforms, as they are called. We manufacture upper platforms for standard 6 DoF Systems or special Motion Systems, such as 3 DoF.
Our frames can be shaped tri-angular or rectangular. Dimensions vary from small frames up to large platforms, which can handle loads over 3.000 kg. Our frames are strong mechanical stiff structures. Upon request, these frames can be manufactured with a custom mounting-hole pattern and, if required, with a coating of choice.
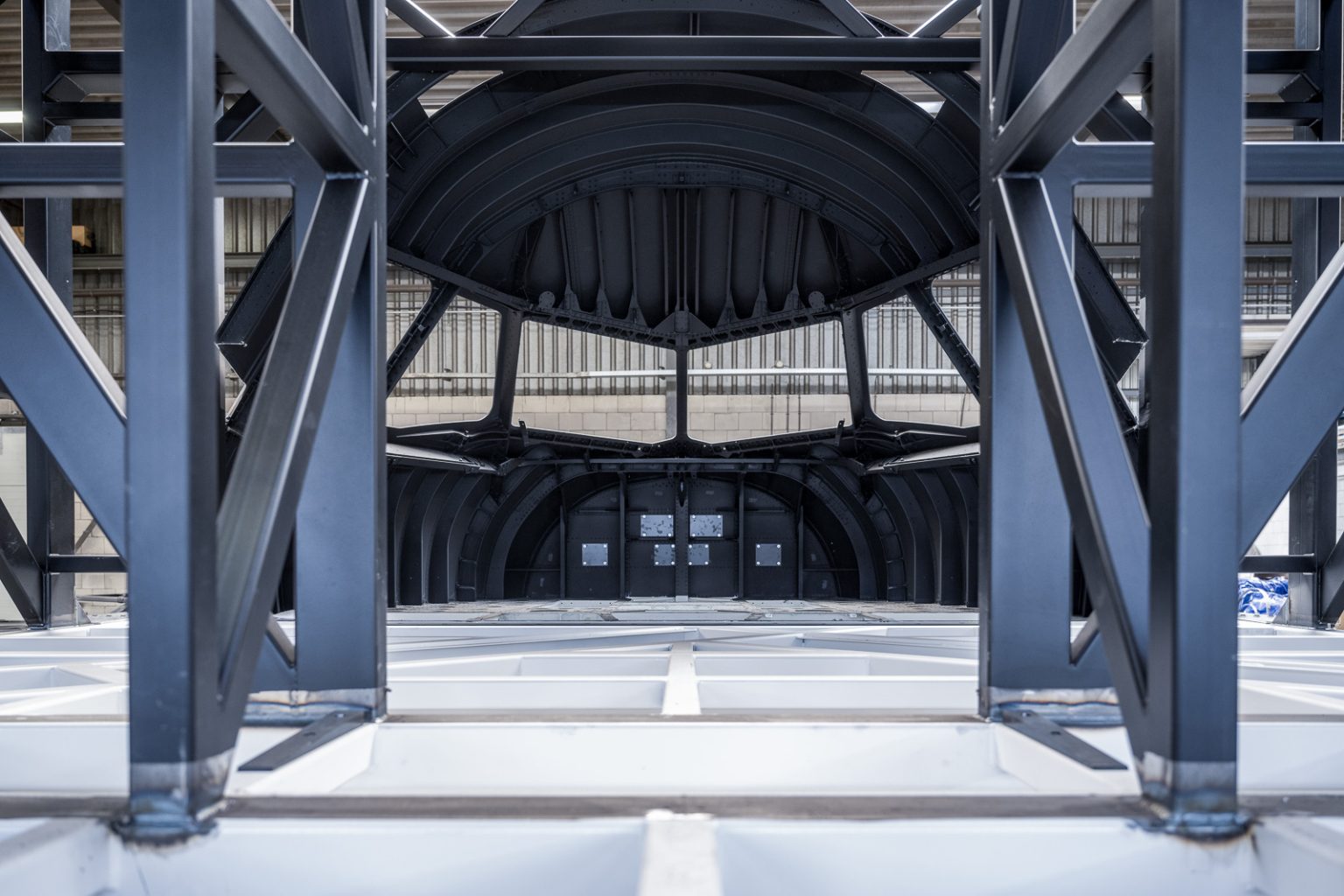
Aft Cabins – or Domes – are placed above the frames. These simulator parts are made from either steel or aluminium. They are rigid and precise structures as they need to support the visual projector system. These visual systems are crucial for a credible functioning of the flight simulator as they provide the images the captain sees while operating the flight simulator.
West End has been manufacturing large frames with tight tolerances and complex geometry for many years. Our machine works cover an area of 5,500 m2. This means we can assemble very large frames. Our working procedures and the support from our own engineering department enable us to manufacture and assemble these parts for simulator. By producing ‘as-built’ drawings, we can guarantee the documentation of product changes. Our order documentation can be used for the cost effective manufacturing of a second series.
Technology
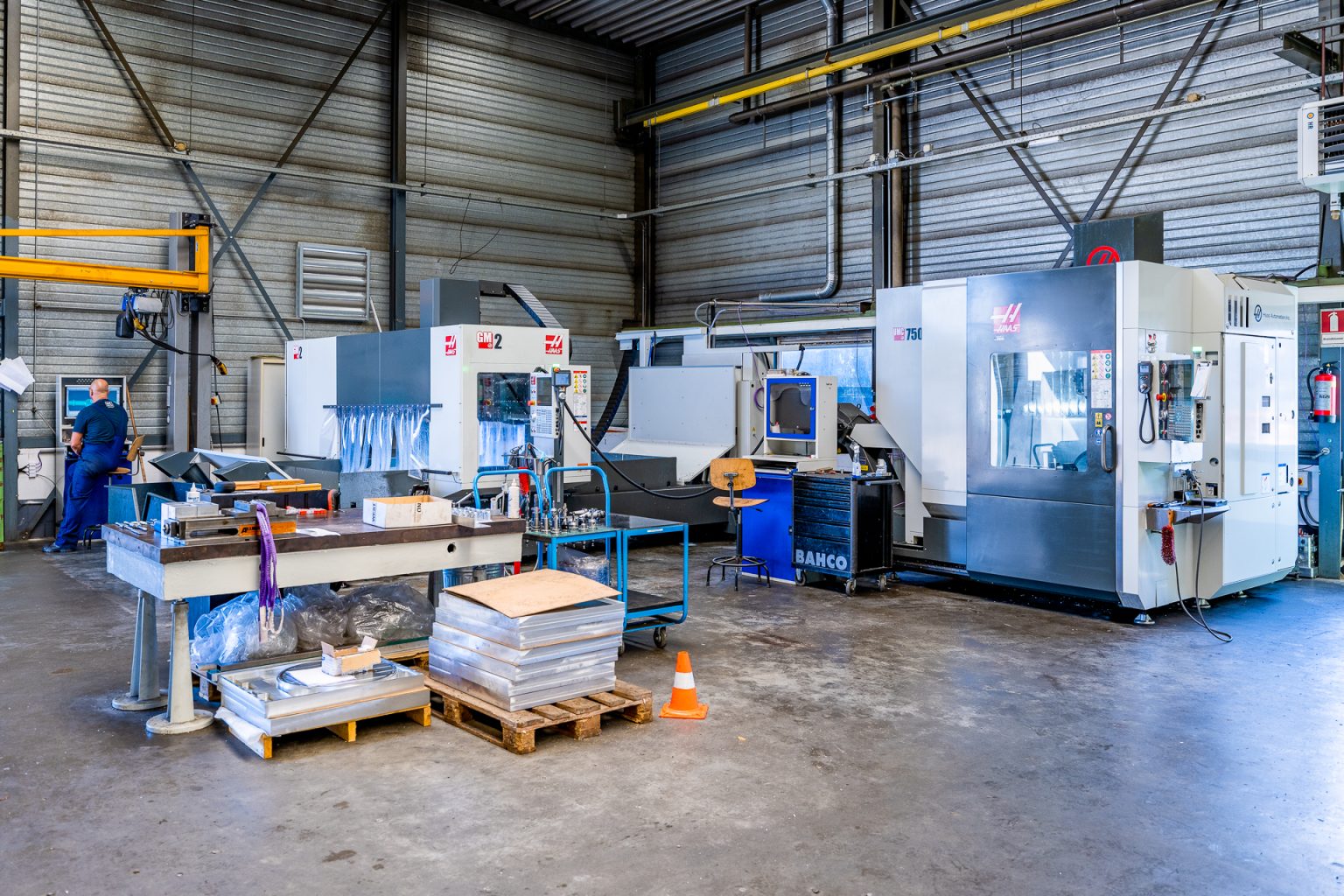
In order to manufacture high tolerance, large parts with complex geometries, West End uses modern CNC machinery. We have a Haas UMC-750 5-axis milling machine and a Haas 4-axis GM-2 large milling portal machine (working bed 4.000 x 2.000 mm).
West End has a EN 1090 certified welding department. Aside from aforementioned and the conventional manufacturing techniques, West End has a cleanroom, 3D measuring equipment and testing equipment for pressure, vacuum and cryogenic applications.
Materials
West End works with various ferrous and non-ferrous metals. Examples are titanium, aluminium, stainless steel, low carbon steel and high strength steels as well as technical
Services
Since 1947, West End specialises in maintenance, repair, modification and refurbishment for a broad range of products.
Our factory has an area of 5.500 square meters and houses almost all necessary manufacturing technologies. West End also has an in-house engineering department. Our team of 6 mechanical engineers is specialised in co-engineering. West End has than 75 years’ experience in manufacturing, maintenance and repairs. With that knowledge, our engineers provide detailed designs and manufacturing drawings, aimed at optimal manufacturability of our products.
In order to improve our service levels, West End continuously invests knowledge, certifications, people and new technology. Our engineering services include 3D modeling, FEM analyses and the production and documentation of 2D manufacturing drawings.
Test facilities
As a true “one-stop service provider”, West End also has a “Test and Assembly” team. This team conducts fit-checks, load tests, shock tests, pressure or vacuum tests for the products we manufacture.
West End has various modern testing facilities for performing Factory Acceptance Tests (FAT). We can carry out leak and vacuum tests in our cleanroom. Of course we can also perform thermal tests for cryogenic conditions or high temperatures.
Our engineering department has 3D measuring equipment, including a modern optical laser tracker for large manufactured products that require a high degree of accuracy.
Our quality inspectors can also use our 3D measurement arm. We use it to check the geometry by probing the geometry of a product, based on the production and working drawings.
Furthermore, we offer our customers to facilitate their test campaigns in our clean assembly department at West End in Lisse.

Secondment
In some cases our service extends beyond maintenance and installation on site. Our people can be seconded to your company for long term and large projects. Moreover, we are always keen to be close to the customer.